
Advantage Analysis of High Strength Carbon Steel Hexagon Socket Screw
Among the many fastener options, high-strength carbon steel hexagon socket screws stand out with their excellent characteristics and wide range of applications. This type of screw is mainly made of high-strength carbon steel, which has excellent mechanical properties and corrosion resistance. High strength means that they can remain stable under heavy loads, and good corrosion resistance ensures that they can be used for a long time without rust even in harsh environments. In addition, the unique black surface treatment not only increases the aesthetics, but also further enhances the anti-rust effect, making the screws also perform well in outdoor environments.
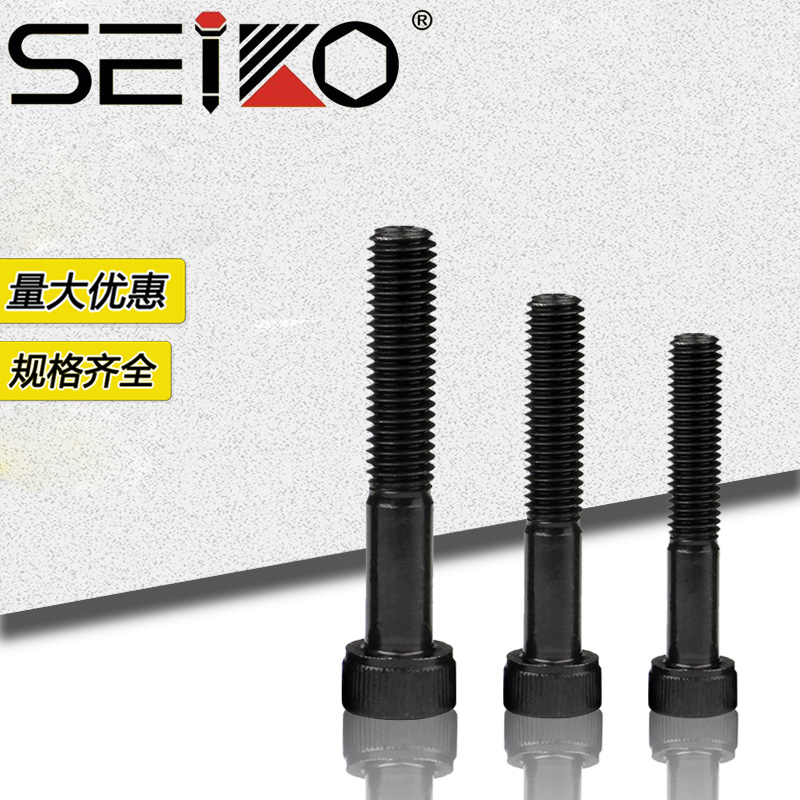
Know the hexagon socket: an indispensable partner
The best partner for hexagon socket screws is the hexagon socket. The hexagon socket is a tool specially used to rotate the hexagon socket screwdriver bit. It is usually made of metal, and the internal shape matches the hexagon socket screwdriver bit. Their design allows more torque force to be applied, thereby easily screwing the screw in or out. There are many types of hexagon socket on the market, but the standard type is favored by users because of its versatility and moderate price. The correct method of use is to fully insert the sleeve into the head of the screwdriver, then gently press it with your hand to ensure close contact, and then turn it.
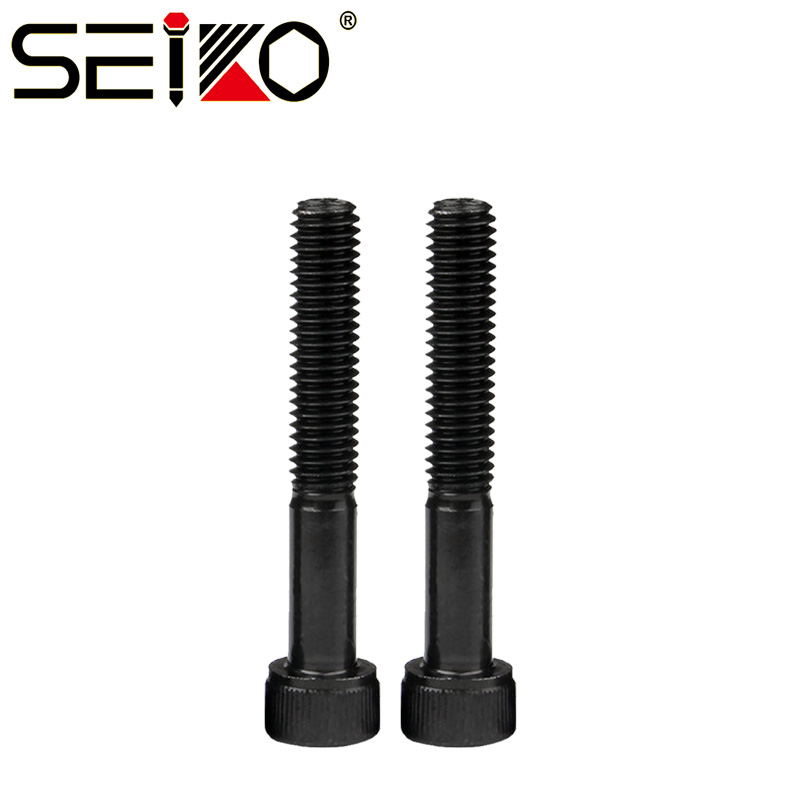
Comprehensively interpret the dimensions of hexagon socket screws
Knowing the size of the hexagon socket screws is essential to choosing the right product. In general, the key parameters of hexagon socket screws include diameter (D), length (L) and pitch (P). The diameter refers to the maximum outer diameter of the thread, the length refers to the distance from the bottom of the nut to the tip, and the pitch refers to the distance between two adjacent threads. In order to facilitate understanding and selection, the following is a table of commonly used specifications:
Diameter (mm) | Length (mm) | Pitch (mm) |
---|---|---|
3 | 10-50 | 0.35 |
4 | 12-60 | 0.7 |
5 | 16-80 | 0.8 |
6 | 20-100 | 1.0 |
8 | 30-150 | 1.25 |
In practical applications, choosing the appropriate screw model requires comprehensive consideration of factors such as the thickness of the connecting parts and the required load-bearing force. For example, when fixing thinner plates, screws with smaller diameters and shorter lengths can be selected; when constructing heavy equipment supports, models with larger diameters and longer lengths should be preferred.
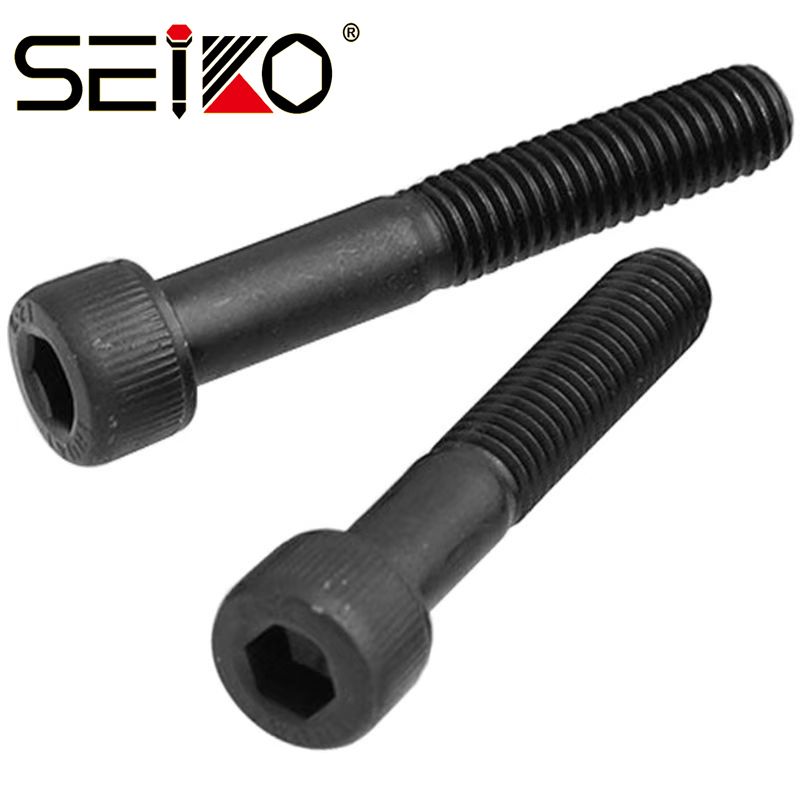
Installation tips and precautions
The correct installation method can significantly improve work efficiency while protecting the screws from damage. First of all, make sure to use a suitable Allen wrench or power tool to avoid slippage caused by size discrepancies. Secondly, before starting the installation, the holes should be properly pre-drilled, especially hard materials, to prevent the screws from breaking. In addition, do not tighten the screws with excessive force to avoid excessive compression or damage to the connection surface. If it is difficult to screw in, you can apply lubricating oil to reduce friction resistance.
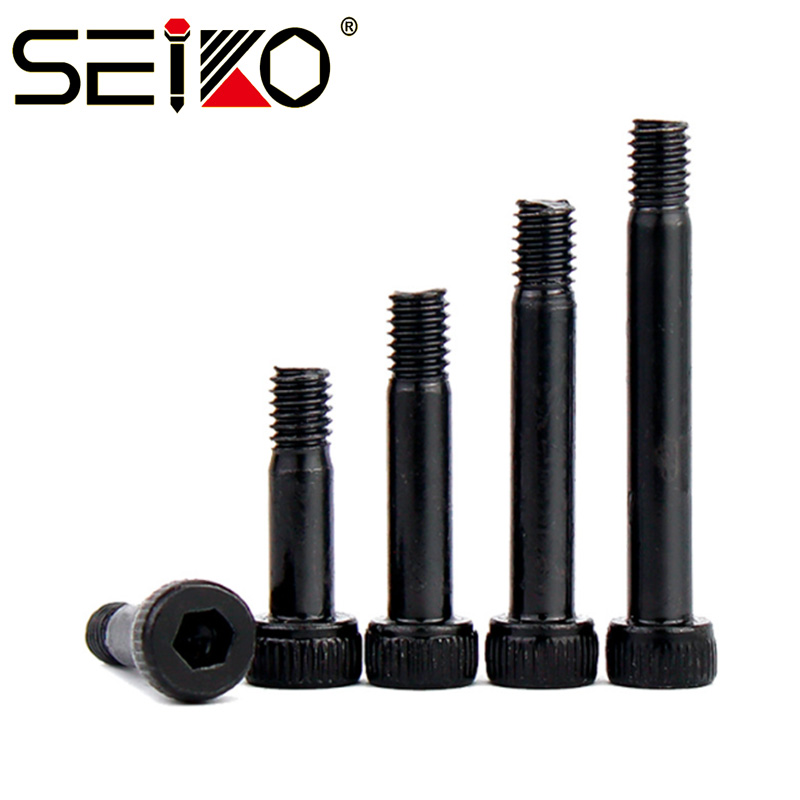
Maintenance Tips
Proper maintenance measures can not only extend the service life of the screw, but also ensure its normal function. Storage should choose a dry and ventilated place, away from acid and alkali substances and high temperature environment to prevent chemical reactions
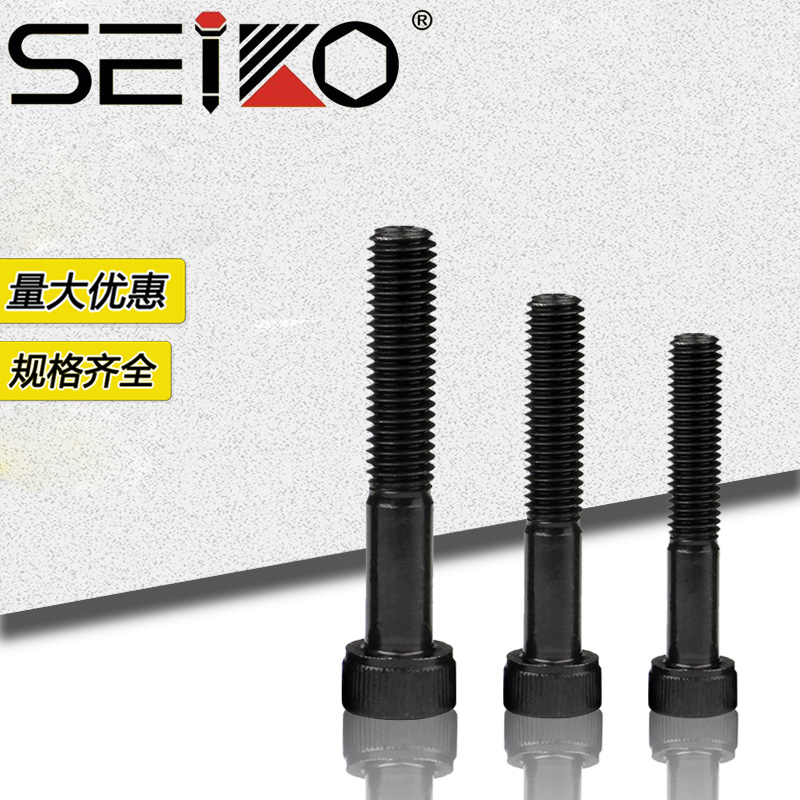